Home > Surveys
SURVEYS
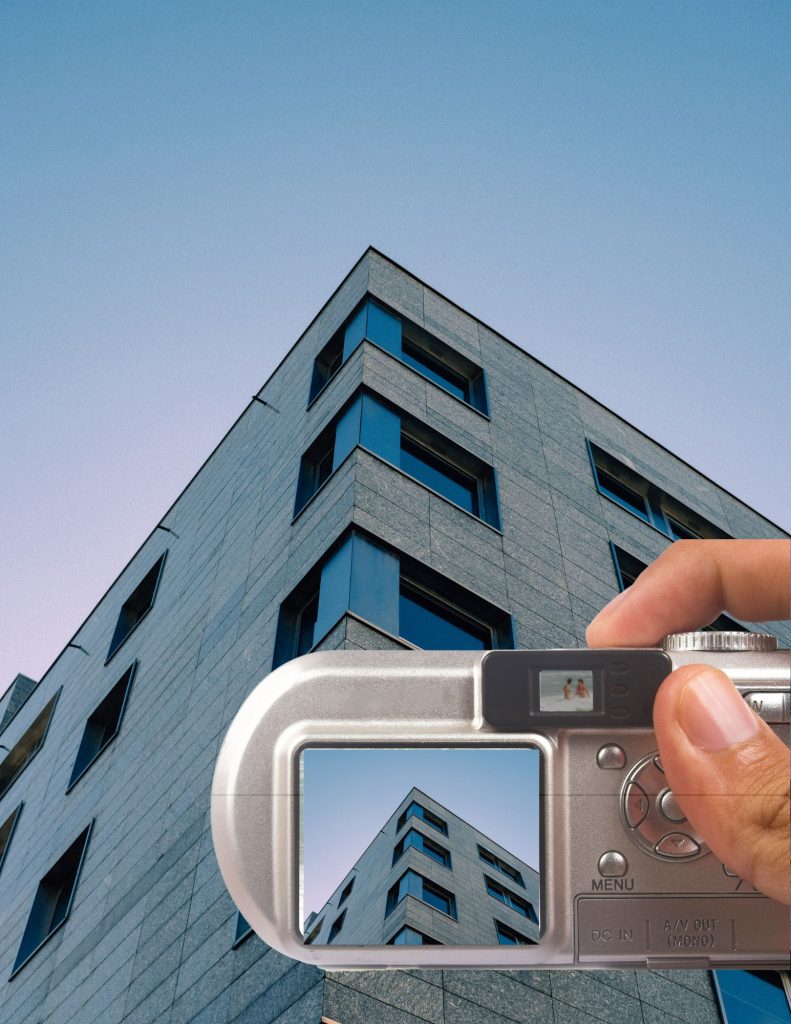
For Property Owners
Have you received a notice offering you a free Pre Condition Survey of your property? Please contact us to make an appointment or request an appointment time online.
Pre Condition Survey
Pre Condition Surveys, a.k.a Pre Construction Surveys, are intended to protect structures and property in close proximity to construction projects. This type of survey protects both parties, the developer and the property owner.
MBI uses a proprietary method to meticulously record the condition of structures. We take high resolution photographs of all accessible surfaces and record existing deficiencies in the survey notes. Our reports provide a detailed and accurate record of the condition of the property before construction activity begins.
Pre Condition Surveys can be beneficial, or at times required, in situations involving:
- Underpinning or encroachment agreements
- Excavating right next to a property line
- Construction activity close to a questionable structure
- Using vibratory compaction without monitoring vibrations
- Litigious neighbours
- Municipal bylaws
- Insurance requirements
- Contractual requirements.
We provide the property owner with a copy of the survey data (photographs and survey notes). We produce a detailed report for you containing the survey notes and a summary of all deficiencies.
If there are any damage claims, we can assist with Post Condition Surveys. In these types of surveys, we repeat the Pre, doing a comparative analysis onsite and in the office, as needed. This type of work is typically only undertaken when there is a contractual requirement or when a damage claim is made.
Contact us for a quote.
- FAQ
A. Pre Condition Surveys are similar to insurance (but less expensive). You don’t need them until something gets damaged. Our survey data ensures that you won’t have damage claims that can’t be substantiated. It is also a good way to set up good relations with neighbouring property owners, especially in residential areas where people’s homes may be impacted by your development.
A. That depends. On our schedule, the size of the survey area and the availability of those providing access. The best thing to do is call us so we can assess.
A. There are many factors that would come into consideration. You would need to consider the type of work that you’re doing. Are you excavating down several stories? Are you working very close to existing structures? Will there be vibratory compaction? Or other construction activities that create large amounts of vibration?
It’s important to assess your liability if something should go wrong to ensure you are sufficiently protected.
A. Yes, you can! Please call us for more information.
Safety Anchor Inspections
MBI makes it fast and easy to have your building’s safety anchors inspected. We provide annual and prior-to-use inspections, as well as Load Tests. Our experienced inspectors work closely with our structural engineers at Arvand Consulting Engineering Corporation to provide you with a thorough inspection report.
To schedule an appointment, call MBI at (604) 435-0710 or email [email protected].
Do you really need an Anchor Inspection?
When your safety anchors were installed, they were certified by an engineer for a 12 month period. WorkSafeBC OHS Regulation Part 11: Fall Protection specifies in 11.9 that anchors must be inspected at least annually or prior to use by a competent person. In addition, the standard recommends recertification of anchorage systems at regular intervals.
The Annual Anchor Inspection
This type of inspection ensures that when you need to have work done on your building, that there will be no delay while you scramble to schedule a prior-to-use inspection. Annual inspections mean that you are able to address any issues with or required repairs to the fall protection system without delaying building maintenance or other projects.
Process
- We schedule a site visit at a time that is convenient to you.
- We will need the onsite contact who will provide access to your roof.
- On the scheduled day and time, our inspector will liaise with your onsite contact for roof access.
- During the remainder of the site visit, we:
- Review and photograph the site map (posted at the entrance to the roof)
- Thoroughly inspect and photograph each piece of equipment for wear, damage and corrosion.
- Note any hazards or issues that need to be addressed
- Detail recommendations, including any required repairs.
- The inspector prepares the detailed report and deliver to the engineer for review.
- The engineer then prepares the certification report.
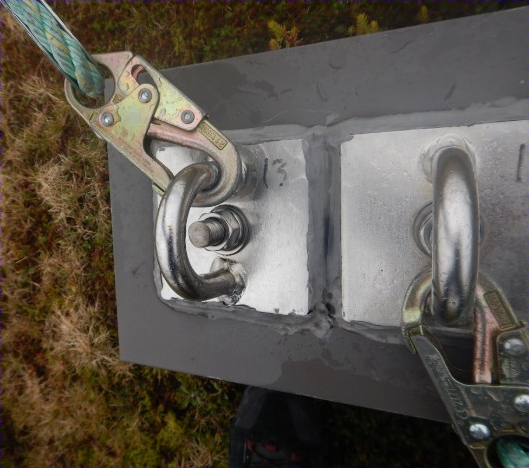
Prior-to-Use Inspections
- FAQ
A. It may be possible to schedule as quickly as the next day, depending on our workload. The best thing to do is call us so we can advise you of our current turn-around time.
A. The photos provide an objective record of the condition of each anchor. This allows us to ensure that any deficiencies from the previous year’s inspection have been addressed. It also means that the engineer can review each anchor in detail as they prepare the certification report.
A. A pull test is required every 5 years for adhesive anchors only. The site map indicates which anchors are adhesive. When we complete your annual inspection, we ensure that we schedule a pull test if required.
- A. Your fall protection system must be certified annually in order to be legally available for work requiring fall protection. If your building is more than 10 feet high, all exterior building work will have to wait until we can schedule a prior-to-use inspection and certification.
A.
All deficiencies noted during the inspection must be repaired or replaced before use. The inspection and certification report details any and all required maintenance. Service providers requiring fall protection cannot start their work until all deficiencies have been addressed.

Infrared Testing
Infrared testing, also known as thermal imaging, is a non-invasive technique used to detect temperature differences in building materials and systems. This method is highly effective for identifying issues such as air leaks, moisture intrusion, electrical hot spots, and insulation deficiencies. By using infrared cameras, we can visualize thermal patterns that are not visible to the naked eye, allowing us to pinpoint problem areas quickly and accurately.
Process
Our trained technicians will conduct a preliminary evaluation of the site to determine the areas to be tested. Using specialized infrared cameras, we scan the building’s exterior and interior surfaces. The cameras detect variations in temperature, which indicate potential issues. The thermal images are analyzed to identify anomalies, such as cold spots (indicating air leaks) or hot spots (indicating electrical issues). After the analysis, we compile a detailed report outlining our findings, including thermal images and recommendations for addressing any identified problems.
- FAQ
A: No, infrared testing is non-invasive and does not require any disruption to the building. We can conduct the survey without moving furniture or altering the space.
A: The duration of the infrared testing depends on the size and complexity of the property. You will be informed of the approximate duration at the time of booking.
A: While minimal preparation is required, it’s helpful to ensure that areas like attics and crawl spaces are accessible, and that there are no obstructions in the areas being inspected
Micro Camera Surveys
Micro camera surveys utilize small, high-resolution cameras to inspect hard-to-reach areas within buildings, such as plumbing, ductwork, and wall cavities. This non-invasive method allows us to visually assess the condition of these spaces without the need for extensive demolition or disruption. By capturing detailed images, we can identify potential issues like blockages, leaks, and structural concerns.
Process
We start with correspondence to understand your specific concerns and determine the areas that require inspection. On the day of your appointment, our technician carefully inserts the micro camera into the designated area through a small access point, allowing us to capture high-quality video and images to assess the condition of the inspected area, identifying any problems or areas of concern. After the survey, we compile a detailed report, including images and findings, along with recommendations for any necessary repairs or further action.
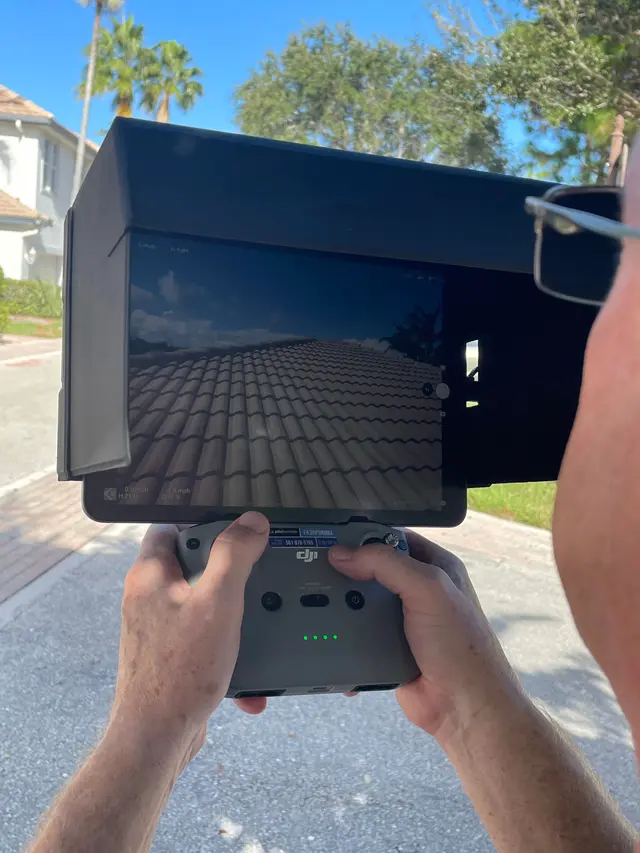
- FAQ
A: Micro camera surveys are ideal for inspecting plumbing systems, HVAC ducts, wall cavities, and other confined spaces that are difficult to access.
A: We can identify blockages, leaks, corrosion, structural damage, and any other irregularities within the inspected area.

Pre Blast Surveys
A Pre Blast Survey is an independent review of the current condition of a home and property. They are offered by blasting contractors to homeowners in the area of a blasting project.
Pre Blast Surveys are required by bylaw in many municipalities and by the contractor’s insurance provider. These surveys protect the homeowner by providing an objective record of the condition of their home prior to any blasting. They also protect the blasting contractor from claims of pre-existing conditions.
A Pre Blast Survey involves a visual inspection of building components. Our surveyor records their observations in a data sheet and with high resolution photographs. The homeowner receives a copy of all photographs as well as the surveyor’s notes. The survey data is also stored on our secure server.
These independent studies are a matter of record and can be referenced by the homeowner or their agent, the municipality, or insurance providers as required.
Accuracy is Important to Us
MBI’s method of recording deficiencies inside and outside of your home is highly specialized. Our surveyors are trained to look for even the smallest detail and to record it accurately. This record then serves as a baseline study of the condition of your property that can be referenced to determine if any changes have occurred.
- FAQ for Developers
A. The first step is to contact your selected blasting contractor. Once you have an agreement with them, the blasting contractor will engage MBI.
We will contact you to ensure you have received your building permit. At that time, we’ll ask for information about where the rock to be removed is located on site. The more detail you can give us, the more precise we can be in our measurements.
We will create a GIS document (map of the survey area) and a contact list. Our process is to mail a Pre Blast Survey notice to each affected homeowner. Our timeframe for completion depends on our current workload, the requirements of the municipality and the response of the affected homeowners.
The process for applying for a blasting permit is a little different in each municipality. MBI can assist by preparing all required documents or we can simply deliver our Pre Blast Survey report when it’s ready and you can take care of the rest.
A. In many cases, we are able to complete all the surveys much more quickly than 6 weeks. There are several factors that may affect our ability to finish faster:
- Affected homeowners don’t respond to our notices or attempts to reach them at home
- Our workload is heavy and we’re scheduling as fast as we can
- One or more affected homeowners is on vacation but insists they get a survey
- Extreme weather conditions.
A. If your project is in the District of West Vancouver, you will need to make adjustments. It is possible to apply for a 15% increase in the maximum allowable if you can justify the increase. Otherwise, the next step is to modify your building plans. Before we can apply for the blasting permit, the building plan modifications will need to be approved.
A. The first step is to have them send MBI photographs of the damage they are claiming, with details of the location of the damage. We can then review the Pre Blast Survey photos to compare. If we can’t identify the deficiency in the Pre photos, or the deficiency has changed, we will recommend to you that you fund a Post Blast Survey.
Post Blast Surveys are a repeat of the Pre Blast Survey with additional review of all areas. Depending on the reported damage, we can assess only the area where the damage is claimed or the entire property. We charge the same for a Post Blast Survey as a Pre Blast Survey. The comparative analysis report is an additional charge.
- FAQ for Home Owners
A. MBI notifies you of blasting in your area and offers you a free Pre Blast Survey. If you choose to have a survey, we schedule a one hour appointment to complete the survey. Some Pre Blast Surveys may take longer than an hour. The time required depends on factors such as the size or the current condition of your home. Our client liaison will contact you the day before your appointment to confirm the time.
A.
Our surveyor will arrive on the scheduled day at the scheduled time. They walk through the interior and around the exterior of your home with you to record and photograph the current condition of your property. Our surveyor records their observations in writing on the data sheets as well as with high resolution photographs.
A.
You will be emailed a link to a folder containing the data sheets and the photographs taken around your property. MBI stores a copy on their secure server. No other party has access to the photographs unless you make a damage claim. At that time, we make the pertinent photographs available to the blasting contractor to demonstrate that the deficiencies were not pre-existing.
A.
Our survey data (photographs and datasheets) are like insurance. They may not seem like much use unless there is damage. There are many factors that can cause damage around your property, so proving damage occurred during a nearby project is not a simple process. With our survey data in hand, you have objective evidence that the deficiency was not pre-existing.
A. We are an independent company. We are contracted by the blasting contractor because they are required by blasting bylaws and insurance requirements to offer these surveys. We’ve developed our proprietary methodology using high resolution photographs and room-by-room survey notes to provide an objective record of the condition of your home. This protects you in the case of new damage. And it also protects the blasting contractor against claims for pre-existing conditions.
A. MBI will survey all accessible areas of your home and property, including foundations, walls, windows, cladding, and hard landscaping. We will survey all areas you provide access to, with the exception of confined spaces. We will not move furniture or stored goods. The survey does not include the roof.
A. For properties within the survey radius, there is no cost to the homeowner. If you have not received a survey notice offering a free survey, but wish to schedule a survey yourself, please contact MBI for fee information.
A. Pre Blast or Pre Condition Survey is like insurance. It’s greatest benefit to you is when something is damaged and you need to make a claim. The photographs are taken of the structure of your home to objectively record the current condition. We do not photograph personal possessions, photographs, artwork or people. If damage does occur, the photographs are the best way to prove the condition was not present before the work began.
A. The length of the survey depends on the size of the property being inspected. A single family home up to 5000 sq ft typically takes 1 to 1.5 hours, depending on the amount of hard landscaping. For larger commercial buildings or multi-residential buildings, MBI will provide an estimate of the time required once the extent of the survey is confirmed.
A. If you notice new deficiencies or old ones that have changed, the first step is to find the area in the survey photographs to see if the condition was pre-existing. The next step is to call MBI to report the condition. MBI will request that you email photographs of the reported condition so we can assess before contacting the blasting contractor. If the condition can’t be identified in the Pre Blast Survey photographs, we then request approval from the blasting contractor to conduct the Post Blast Survey.
A. We recommend that you contact MBI. We will contact the contractor on site. Depending on the type of project, the contractor will take steps to address your concerns.
- Blasting FAQ
This information was originally published on The World of Explosives website
A: Most of the energy from a blast is used to break rock, but some energy will travel from the blast site in the form of ground and airwaves. Each of these can cause your house to vibrate or shake. Humans are very sensitive to all vibrations. It is possible that you will feel or hear your house shake from the blasting, even at very low levels.
A: How a blast feels depends on ground or airwaves that reach your house. These are influenced by the type of blast, the distance from the blast and the amount of explosives.
Your location on the property also affects your perception of the blast. If you are outside a house, you will tend to feel the ground vibrations in your feet and legs. Inside a house, you sense the structure and objects responding to the vibrations. You may also hear objects rattle. This is why you and your neighbors may feel or describe blast vibrations differently.
A: Typically, blasters are licensed professionals who are required by regulation or by their employers to continually obtain training. They are trained to plan, design, implement and monitor blasts. This training stresses safety in all aspects including protection of your property.
Prior to blasting, pre blast inspections/pre blast surveys may be offered to nearby property owners to document the existing condition of buildings and identify any sensitive structures, building components or contents. The site conditions and the inspection information are employed to design the blast to minimize effects to your property.
To ensure that the blasts are working as planned, the resulting ground and airwaves can be measured with a blasting seismograph.
A: A blasting seismograph measures and records the ground and airwaves from a blast. The information is reported as waveforms, also known as time history records. Time histories show how the strength (amplitude) of the waves varies over time. Amplitudes are reported as particle velocity (inches per second) for ground waves and pressure (pounds per square inch) or decibels for airwaves.
Another important characteristic of the time history is frequency. Frequency is the number of complete waves that pass by in one second. It is reported in cycles per second or hertz. Both amplitude and frequency are needed to describe the motion from ground and ai waves.
The blasting seismograph information is used to show compliance with regulations or specified limits and to evaluate blast design performance. Most importantly, it verifies that the ground and air vibrations are within standards set to protect structures.
A: In North America, safe vibration standards are based on scientific studies conducted by the U.S. Bureau of Mines (USBM). These studies recommend ground and air vibration limits based on scaled distance, peak particle velocity, air pressure and frequency. Meeting these standards will prevent even cosmetic cracking in structures. On the other hand, slightly exceeding these conservative standards will not necessarily harm a structure.
For ground vibrations, the standard is a function of frequency and peak particle velocity. At low frequencies, the limit is 0.5 inches per second (in./sec.). At high frequencies, the limit is up to 2.0 in./sec. For the best representation of the standard, see the graph showing the USBM recommended limits.
For air vibrations, the standard is a function of pressure that is most often reported as decibels with a common limit of 133 decibels (dB).
A blasting seismograph is one tool that can be used to document compliance with these standards. Another method sometimes used is a minimum scaled distance which is a relationship of explosive quantities and distance.
A: No. Blasting seismograph data is stored digitally and coded internally to prevent tampering. The data is printed with proprietary software from the manufacturer.
A: Research has shown that it is more consistent to measure the ground waves entering the structure. Therefore, the seismograph sensor is attached to the ground outside your house. By installing the sensors outside, the measured vibration levels can be compared with known safe limits, existing regulations or industry standards.
A: The two scales are not related and cannot be interchanged.
A blasting seismograph simply reports how much the ground vibrates in one particular location. It measures the intensity of ground motion. This measured intensity will be stronger if the seismograph is close to a blast and lower if the seismograph is far away. In blasting, the unit of measurement we use to describe this motion is peak particle velocity.
The Richter Scale reports the power of an earthquake or its magnitude. It’s an estimation of the energy released at the source. In blasting, it would equate roughly to the total weight of explosives used in a blast.
Earthquake scientists do use seismographs to measure the intensity of the ground waves at different locations and then calculate a Richter Scale magnitude. This value is based on two things: how far the seismograph was from the earthquake and the intensity of the ground waves at numerous seismograph locations.
A: Ground waves change as they pass through different kinds of materials, and in general, the strength (amplitude) decreases rapidly as it moves farther from a blast. This happens regardless of whether they follow the same rock layer or whether that layer changes. As these waves reach your property, your house will be protected if the strength of the vibrations are within allowable limits. These limits are conservatively set to protect surrounding houses regardless of the underlying material.
A: The foundation is the strongest part of a house. Vibration standards are designed to protect the weakest parts of the house, such as plaster and drywall. Ground vibrations strong enough to crack foundations consisting of concrete and masonry would far exceed the limits set by typical standards.
A: Below-ground structures are confined in the ground and can only move as much as the ground itself moves. They respond less to the ground waves than a house or other buildings above ground. Therefore, standards that protect houses will also protect below-ground structures.
A: Only unusual soils like very loose, saturated sands are susceptible to settlement from ground vibrations. Even where these soils are present, typical blasts do not create conditions which cause settlement due to the short duration and relatively low amplitude of the ground waves.
A: Vibration energy is not stored in the house and has no potential to be cumulative. Each blast affects your home as a single event and rarely lasts for more than a few seconds. As ground and airwaves pass, the house will begin to vibrate. When the ground and airwaves end, the house will stop vibrating and there will be no further effect from the blast.
A: This question relates to the concept of structural fatigue, which has been studied by the USBM. In one study, a house was intentionally shaken to find the fatigue limit. Over 50,000 cycles of motion were needed to cause a cosmetic crack. For most blasting projects, the total number of significant ground wave cycles reaching a house is fewer than 1000. Vibration limits have been set accordingly.
A: The pre blast survey protects both the homeowner and the blaster by documenting the condition of the home before blasting. After blasting has started, any suspected changes that are found can be compared to the initial condition.
A: An undocumented crack isn’t necessarily the result of blasting. There are other factors to consider in determining whether blasting caused any crack. For example, environmental effects such as temperature, humidity and wind, as well as homeowner activity may contribute to cracking. On rare occasions, a crack may be the result of blasting if ground or air vibrations exceed recommended standards.
A: A blasting specialist needs to look at the blast and seismograph records to determine the intensity levels of ground and air vibrations at your home. Based on the estimated or recorded vibration levels at your house, as well as other factors, it can be determined whether blasting could have been responsible.
A: There are many possible causes. Every day, construction elements of your house shrink and swell from environmental changes. And movement occurs from human activities such as opening and closing doors and windows, hanging pictures on a wall or simply walking through the house.
Continued research has shown that changes in temperature, humidity and soil moisture can yield greater changes to a structure than ground and air vibrations from a blast that are within recommended standards.
A: Pets, like humans, are sometimes startled by the sound of a blast or warning signals, just as they might be startled from thunder. Like humans, animals are subjected to a variety of vibration sources and events each day with no long-term effect.
What Are You Guaranteed When You Choose MBI?
Choosing a company to fulfill your project needs can be overwhelming. There are so many aspects to consider. To save you some of the guesswork, MBI offers several key benefits with our services.